Hi Ego. I love the pictures of your restoration lab you've shown over the years. Your areas look like a museum restoration lab.
Here is my workshop area. Looks cluttered. It is well organized for the jobs I do. I try to think things out when I set up but I have limits on space and money. This is my compromise that I came up with.
There's tool storage and workshop setup. They are related but not quite the same. I can store away all my stuff meticulously in boxes with an accompanying database to find everything. That isn't terribly efficient for work. If I put everything out I need too much space. So there's this balance.
To strike the balance I set up based on hierarchy of use. My favorite most used tools are on the rack. Less so are on the pegboards. Specialty tools are in the boxes above and below. It's all based on how fast I need to access them. When deciding on "a home" for a particular tool I close my eyes and think of the first place I'd look for that tool. Usually what comes into my mind in the first five seconds is the logical place for it to live. I then put it there. Label the boxes. Segregate the boxes by type of tool.
Stuff like welding equipment, sheet metal tools, air conditioning tools, suspension rebuild equipment, wheel alignment fixtures etc. are rarely used and are stored away in the loft above and on shelves out of the field of view. These images are the central focus based on the work I'm focused on.
I spent a lot of time building R&D labs and manufacturing lines. We could over organize to the point that we became inefficient. It's like filing systems. You want to file well enough so you can find the document in the acceptable period of time balanced with how often you access it. I had some Kaizen engineers help me in the past. You can learn a lot of workshop philosophy from them. The goal is to boost efficiency of all types - production, containment and money.
Kaizen has some really good philosophy for shop setup and tool storage. I suggest you look there if you're serious. I really switched up my work areas after I got schooled by a couple of Kaizen engineers. They really know how to make an efficient working shop.
ETA - I was really messy up to age 30. My labs, closets, files, designs, research and workshops were disaster areas. I met a mentor who really convinced me that I was programming in inefficiency through disorganization. Up to then I lost everything, papers, tools, unused supplies and valuables. Organizing my tools and systems really made things more efficient. Not easier. I was able to manage a more complex system and produce more with the same amount of energy and space. Not wasting your duty cycle searching and retrieving stuff allows you to allocate more cycle to process. It took about a quarter to transform my life using well engineered systems of organization. My designs got a lot better too - more complexity, more manageable, less anxiety.
And there’s a lesson there too. My mentor was a great digital systems and software designer. But he over did the organization part. He over filed stuff. He spent so much time planning the systems surrounding the systems that his scope got severely limited. Like he wrote so much documentation that you’d give up on following his design because it took too long to read through. Or there’d be so many sub folders or sub compartments to his organizational hierarchy that you’d just get lost deep in a design. But his spirit was right in that he saw organization as an efficiency tool to control complexity. Too rigid a guy though…I can Google him and see he never reached his lofty goals. I think he spent too much time organizing.
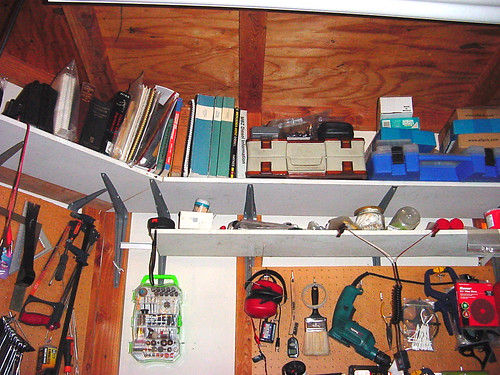